A Serbian Manufacturer Finds Their IT Backbone to Transform Operations
Cisco
Starting over is challenging, and many businesses choose short-term solutions when retooling their operations or rewriting their procedures. They’re either unwilling to commit to a long-term vision or trying to minimize costs by budgeting for solutions that will only see them through the next few quarters. This short-sightedness, while cost-effective, can hinder a company’s future.
That’s why Wacker Neuson is taking a long view and a multi-phase approach to building and outfitting our new factory in Serbia. We could have moved equipment from our other plants and upgraded slowly over the years. However, the initial savings would have been offset by our inability to leverage new technology to build capacity and streamline workflows at our new production facilities.
A Historic Factory Expansion
Wacker Neuson is a leading manufacturer of steel components, construction equipment, and compaction machines, offering our customers a broad range of products, services, and an efficient spare parts supply. Our HQ is based in Munich, Germany, and employ over 6,000 people worldwide, with an annual sales volume of €1.71 billion.
In 2022, we embarked on our first expansion project in 15 years: a new 20,000-square-meter factory to replace our existing facility in Kragujevac, Serbia. This €26 million investment will create 200 new jobs, and a future project phase will see the facility expand to 50,000 square meters.
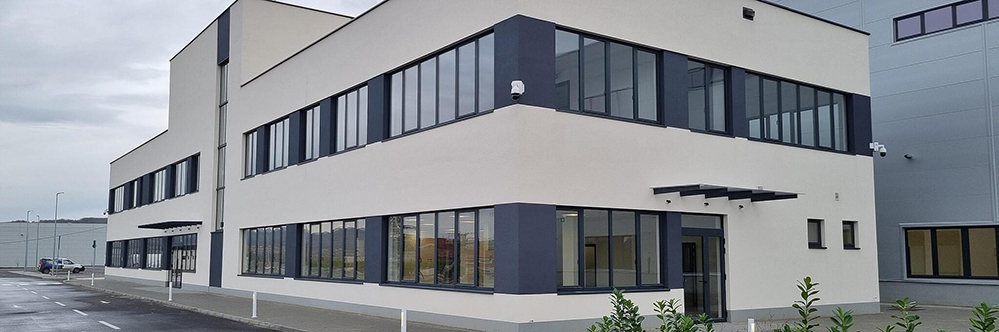
I started working for the company in December 2020 as an on-site IT specialist. I'm a contact point with our corporate IT department and provide front-line support for the transition. I also contribute to the procurement process and am helping our head office cost the IT infrastructure for the future expansion of our new plant. My mission is to improve my IT skills and acquire new knowledge to best support our infrastructure and the IT department’s quality of service. I especially wanted to improve my knowledge of network administration because we experienced a lot of network problems at the old facility.
At the time, these problems were hard to diagnose, and we were also dealing with a lot of issues. Factories are noisy, dusty environments, and our network switches were installed in racks near heavy machinery. It was far from optimal—vibrations can loosen connections, and dust can damage fiber optic cables and clog the ports on switches. Manufacturing facilities aren’t like offices, and the network hardware should reflect those differences. When we started planning the new factory, we decided to purchase industrial-grade hardware that was reliable, highly secure, affordable, and could withstand factory floor conditions.
We Based Our New Network on Cisco Technology
We chose Cisco because the company is a global technology leader with an extensive portfolio of network hardware and software solutions. They also provide outstanding support, including local support backed by the company’s international team. Unlike other vendors, their teams and partners speak our language (and are in our time zone), we're troubleshooting during our normal day instead of extended evening hours. This level of support is essential in a partner who will help see us through the next few years of expansion.
We worked with Serbian Cisco Partner Roaming Networks to architect a network that will serve two primary functions at our new factory. It will serve as the backbone of our SCADA (Supervisory Control and Data Acquisition) system that will automate our production line and heavy machinery and serve as our wired and wireless enterprise LAN. The network uses Cisco Catalyst switches and Meraki MR36 Wi-Fi access points. All three are highly secure, cloud-managed, and energy-efficient. The Catalyst switches are stackable and rugged enough to withstand factory floor conditions, and the Meraki access points provide fast wireless connectivity with dashboard-based management. Everything can be remotely configured, greatly facilitating system maintenance.
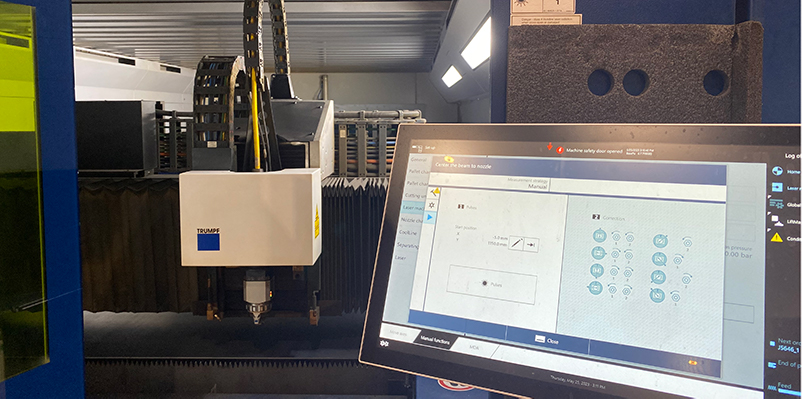
When we started planning our network, I worked with our corporate IT team and Roaming Networks to architect, fine-tune, and deploy the solution. In the end, it took one day for the Roaming Networks team to install all the hardware at the new factory with remote support from our corporate office. We deployed 25 Meraki access points on the factory floor and five in our administrative offices. We installed two Catalyst core switches, one in each of our server rooms. We also set up 30 Catalyst basic switches across our operations, including two stacks in the server rooms, another 10 in production, and a switch at our Gatehouse. Everything is connected via a fiber-optic ring.
Our New Factory Will Inspire Bigger Plants Across Europe
The Kragujevac facility is one of Wacker Neuson’s smaller production sites, but this Serbian location will serve as a testing ground for factory automation. Our new Cisco technology behind the heavy machinery, SCADA and IoT integrations, and network will provide a template for future deployments at larger sites, like our plants in Munich, Germany and Linz, Austria. It’s an opportunity for our factory to write the playbook and set the standards everyone will adhere to in the future. On a personal note, it is an incredible opportunity to learn more about automation and IoT, two areas that are new to me.
Serbia is a central European manufacturing hub, and Wacker Neuson is one of many international companies that have established manufacturing facilities here. Our new plant will allow us to better leverage the skilled labor pool and industrial and transportation infrastructure available in Kragujevac. A state-of-the-art factory, it features cutting-edge automation and adheres to international health and safety, environmental, and manufacturing standards. It is clean and efficient and allows us to stand shoulder-to-shoulder with our peers in Germany, Austria, USA, and China. It will also help us speed production, eliminate bottlenecks, and reduce the risk of stoppages. There’s no comparison to the plant it replaces; we’re taking everything to the next level.
I’m always learning and upskilling. I passed my CCNA qualification exam last year, and my CCNA training will help me during our continued expansion. Even though I am one of just two front-line support workers, we have the power of the Cisco team, Roaming Networks, and our corporate IT team behind me to maintain our infrastructure and keep production flowing. There are many moving parts, but Cisco is the glue that holds everything together. Starting over was tough, but we faced only minor difficulties installing and configuring the Cisco network at our new facility. Our production environment is now fully deployed, and the factory went live at the end of April 2023.
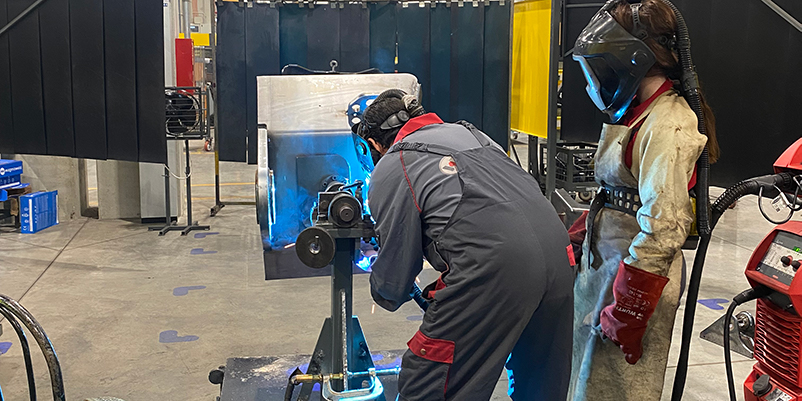
Our Initial Investment in Cisco Paid Off
Sure, we could have saved money by repurposing equipment from the old factory or installing a less capable network with fewer features and just enough capacity to meet our immediate needs. Instead, we chose Cisco technology that is easy to manage and sets the stage for future growth.
Next year, we’ll more than double the size of our factory floor (phase two), adding more Cisco technology like industrial switches and heavy machinery to our production environment to power more automation while increasing and speeding our output. Phase three is already in the planning stage as we pursue our aggressive expansion strategy.
Cisco gave Wacker Neuson a powerful, flexible IT backbone to build a model factory that will transform our Kragujevac operations and inspire future plants across Europe.